From flax seed to linen yarn
The majority of our range of fabrics are woven from linen. They are woven from linen from the area in northern Belgium and France. The range is from thin and delicate voile to heavy furniture fabrics. One of the major advantages of using linen is that the whole process from growing through to preparation of the fibres is sustainable. All parts of the flax plant are biodegradable and the linen fabric is recyclable, making it one of the most sustainable raw materials in the world.
All parts of the flax plant are biodegradable and the linen fabric is recyclable, making it one of the most sustainable raw materials in the world.
Growing flax requires no irrigation to be compared with cotton, which requires no less than 9000 litres of water for a yield of 1 kilo. Furthermore, flax requires very little fertilizer and pesticide. The Linen that we use in our products is grown, harvested and spun in northern France, Belgium and Holland. The fabrics are then produced in textile mills in Belgium, Spain and Italy. Growing flax or linseed and then spinning and weaving it is an age-old craft in these parts, and we are very happy and proud to be part of sustaining the tradition.
Even in Sweden, there is a strong culture and tradition surrounding the use of linen, mostly in the province of Hälsingland, where we still can see the traces from linen heydays in the form of the beautiful Hälsinge farms that remain. The rich soils produced high yields of flax while the abundance of water powered the mills that, in many cases, employed hundreds of people. The factories supplied linen fabrics to the Courts in Sweden and Europe and made local farmers rich enough to build impressive homes, some of which are still standing and are now World Heritage sites.
Unfortunately, Sweden is no longer home to large scale flax farming, but a few mills, such as Klässbol and Växbo lin, still produce linen fabrics.
Growing and processing flax
The flax seeds are sown in early spring and after approximately 100 days, the plants are about one metre tall. They then bloom at the end of June. The plants are harvested, roots and all, and placed in neat rows in the fields. After harvest, retting takes place. The linen fibres slowly soften, making it possible to extract them from the outer husk. The plants are placed directly on the soil, which contributes to the beige tint of the linen. The duration of the retting process is highly dependent on the weather. It takes great knowledge and plenty of experience to be able to determine when it is complete. At the end of the retting process, different colour variations are determined and earmarked for the production of different fabrics.
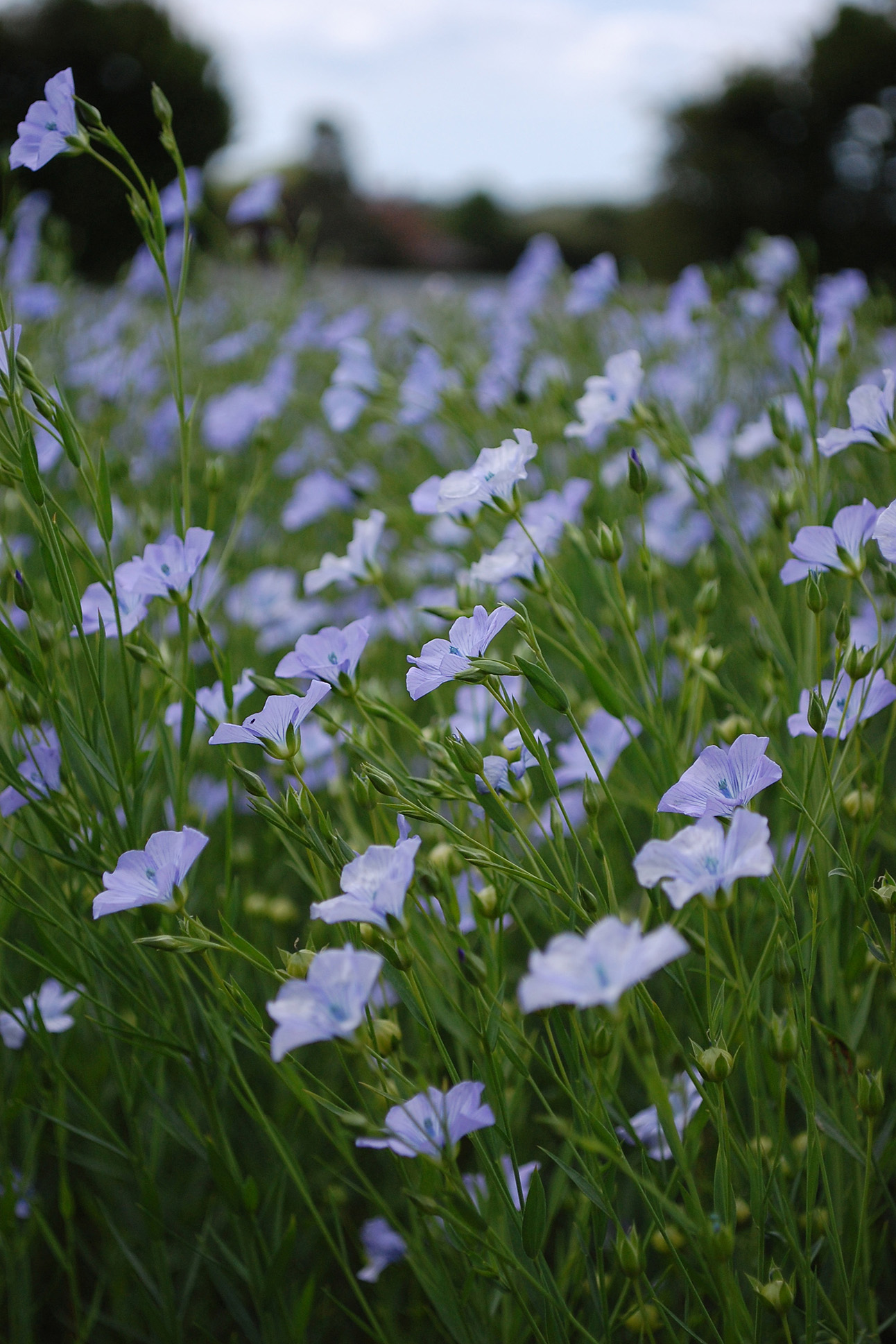
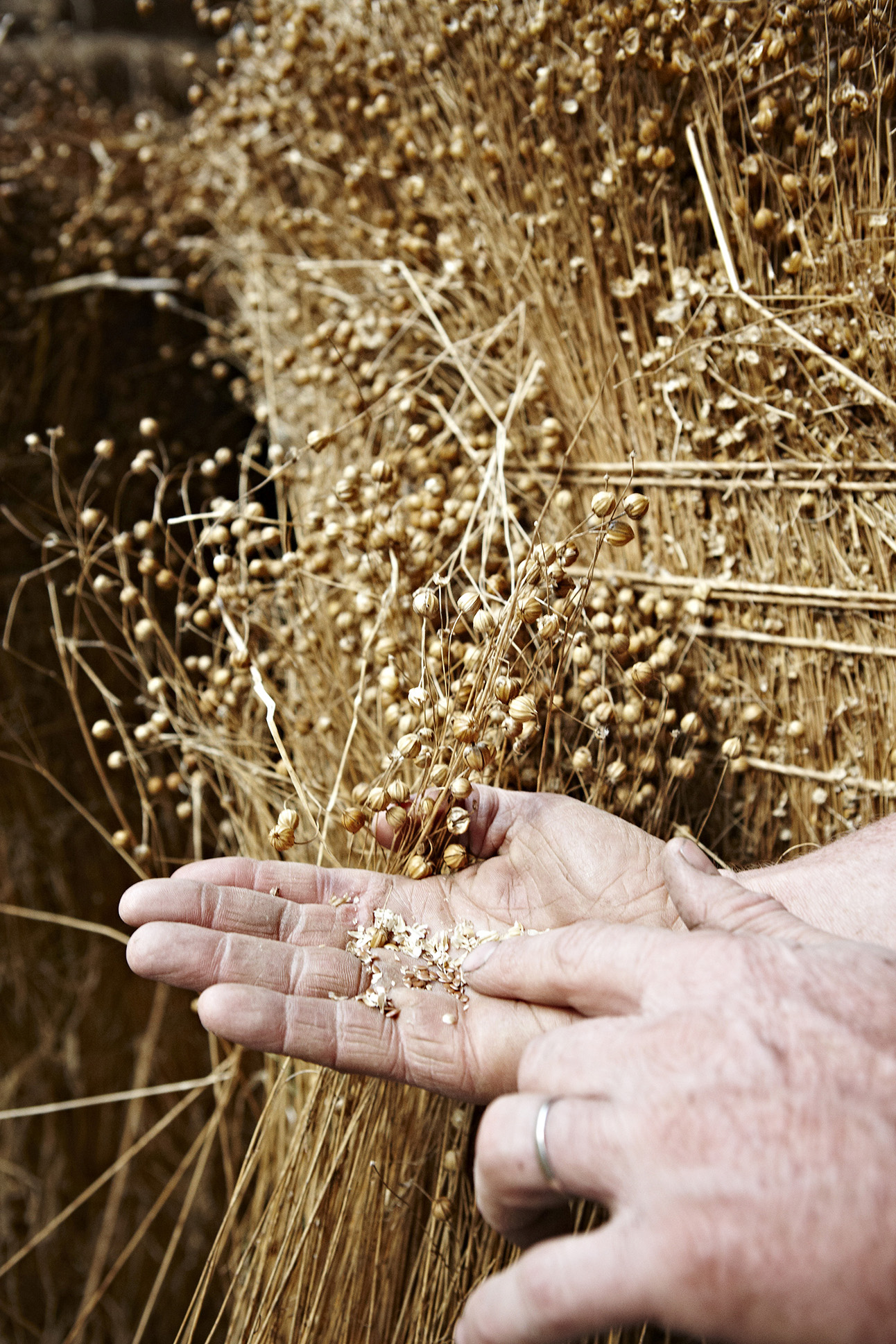
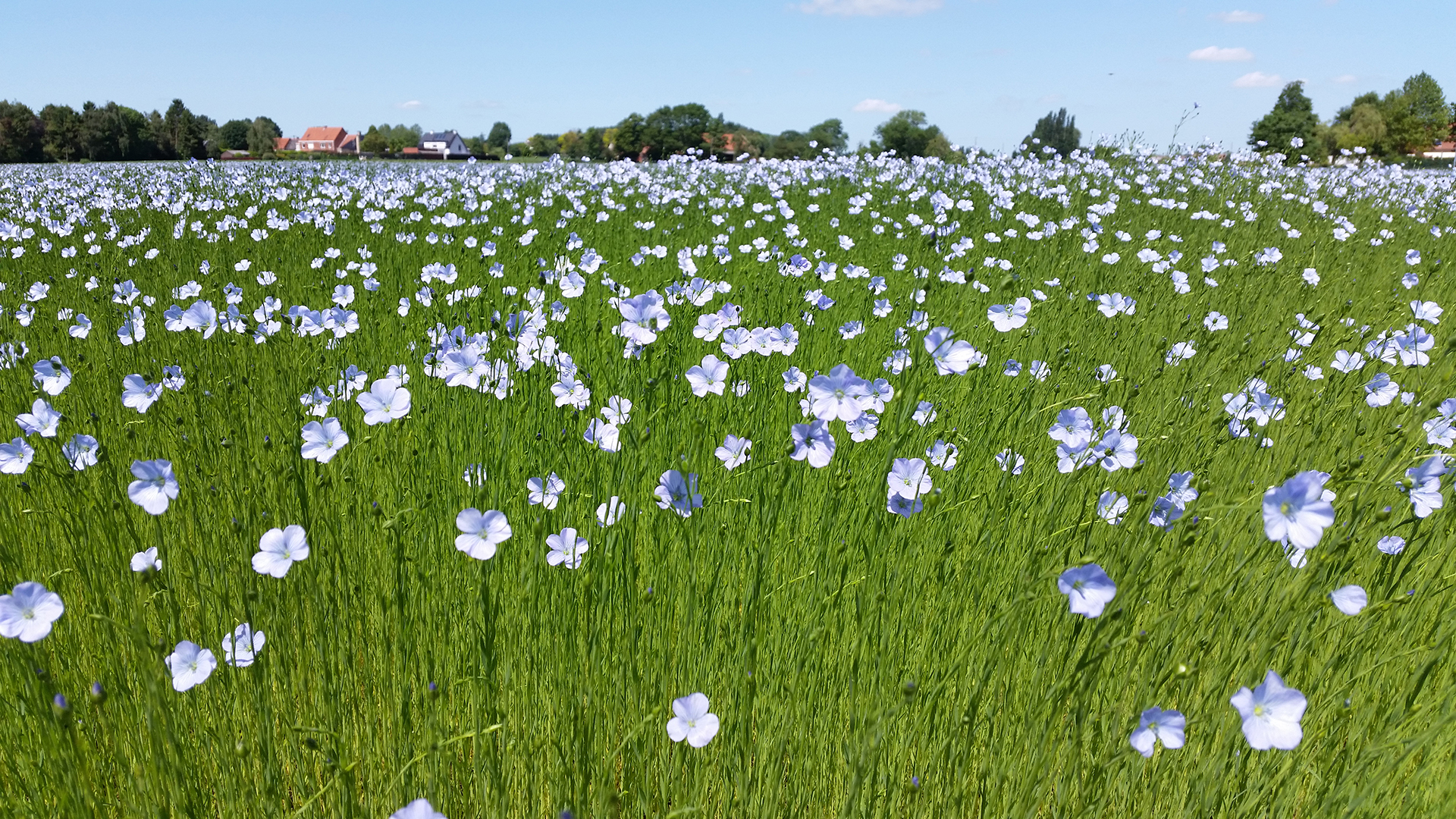
The plants are then rolled into large bales and brought inside in order to start the process of separating the delicate bast fibre. In the first step, the core of the plant is crushed in a process called scutching, in order to access the desirable bast fibres.
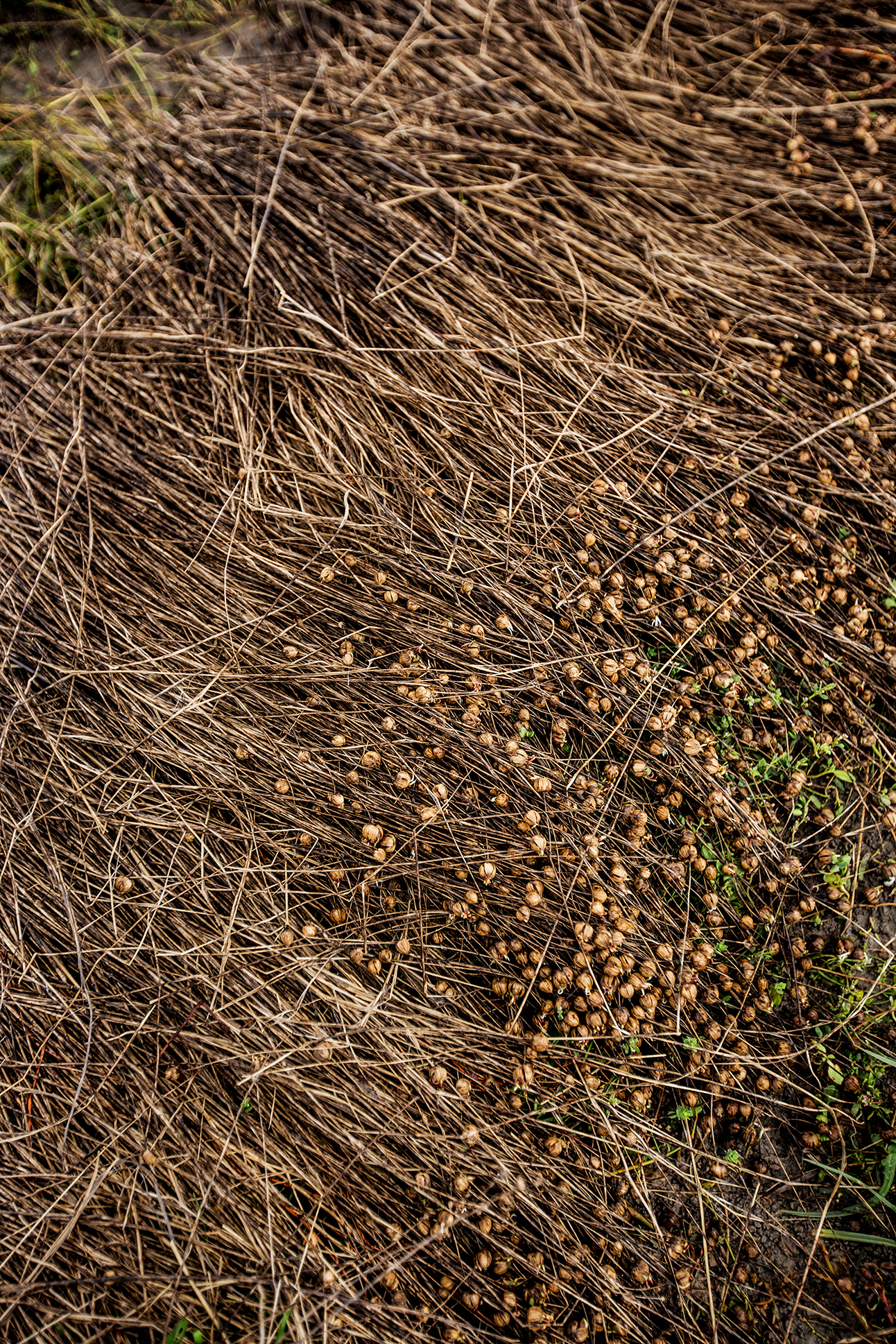
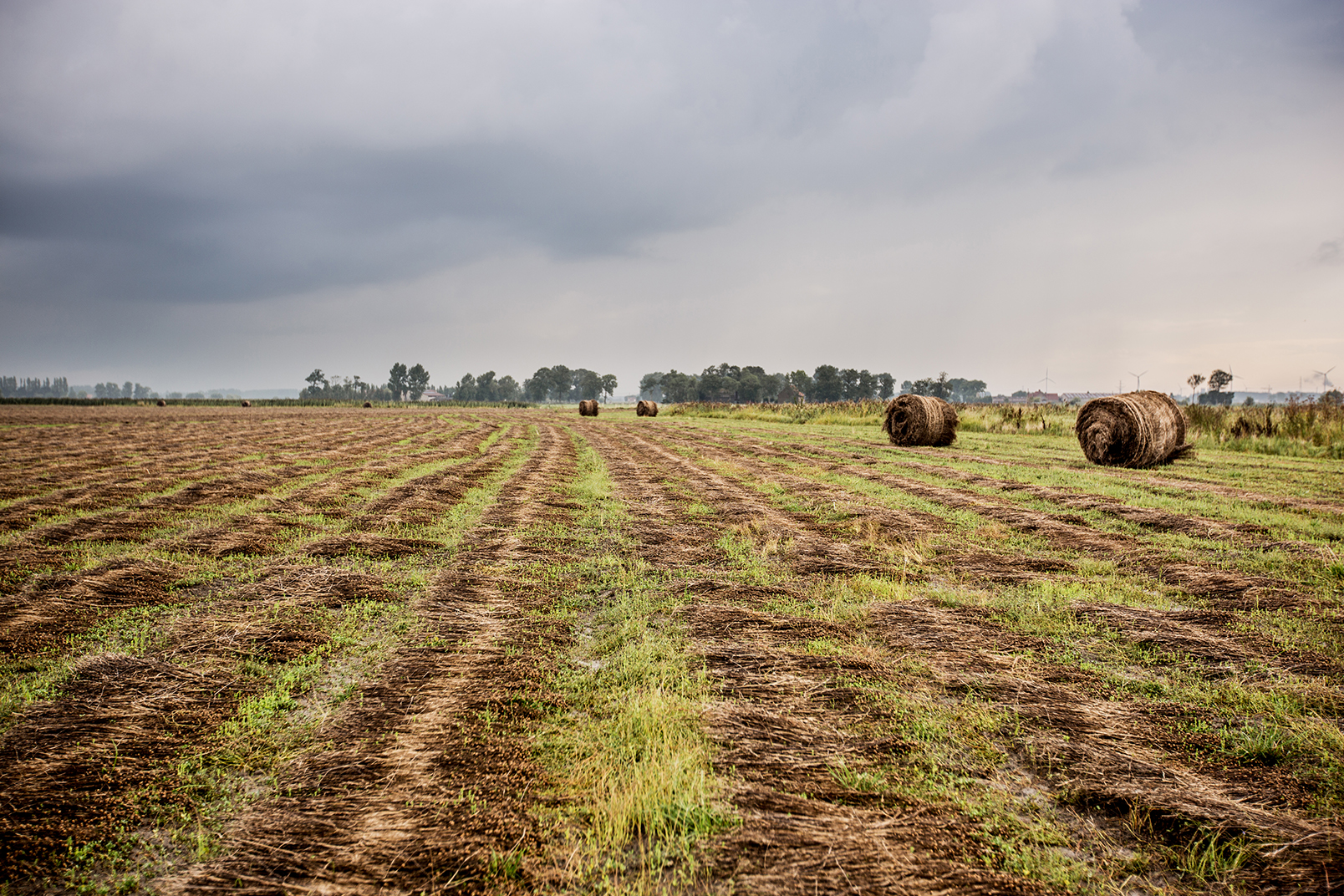
The next step means that the rest of the husk is removed from the bast and may be used for plywood or straw. Through a process called hackling, the long fibres are separated from the short ones, using a kind of steel comb. The final step of the process is spinning the fibres into linen yarn. The long and fine fibres are used for thin yarn and the shorter fibres become coarser yarn.

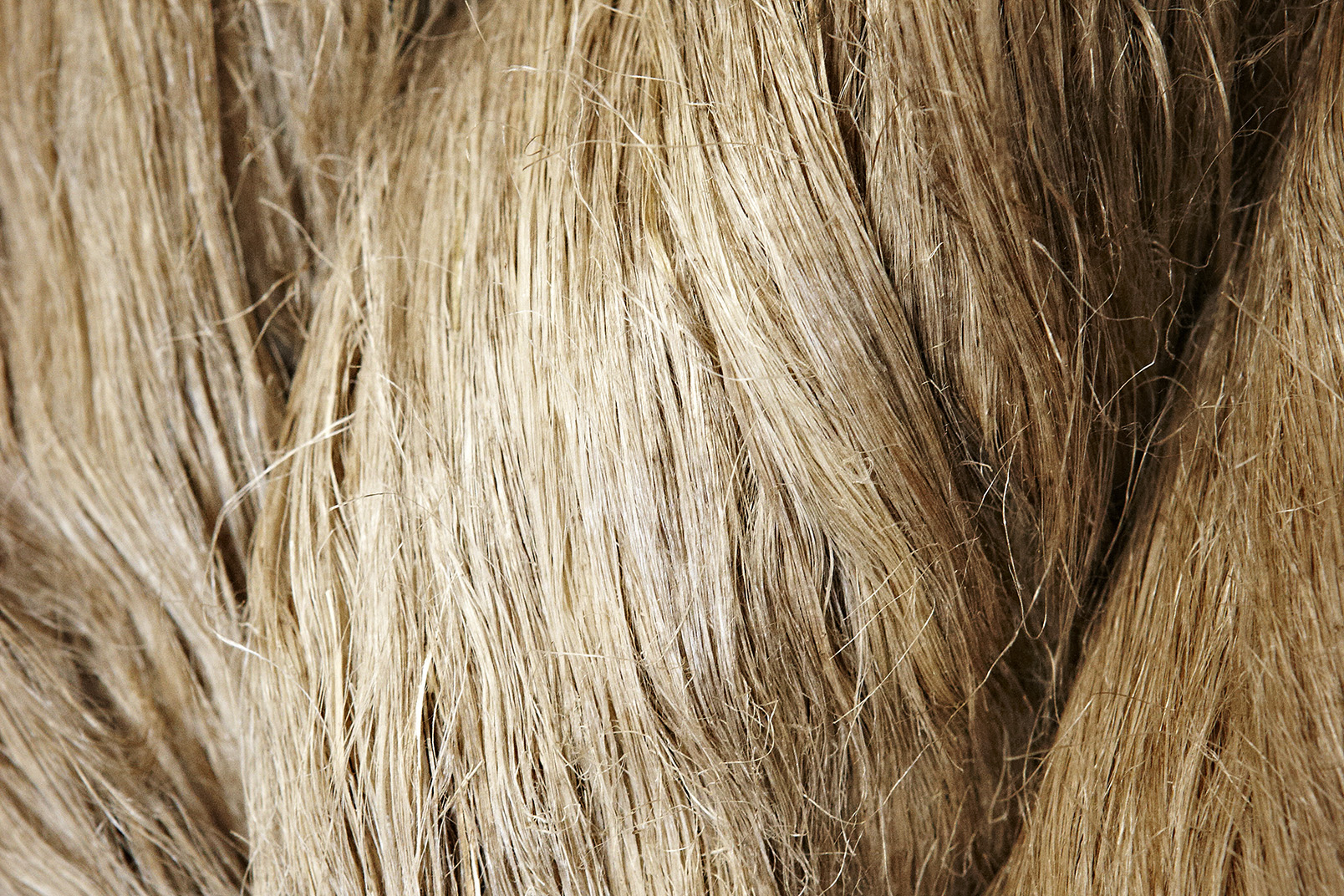
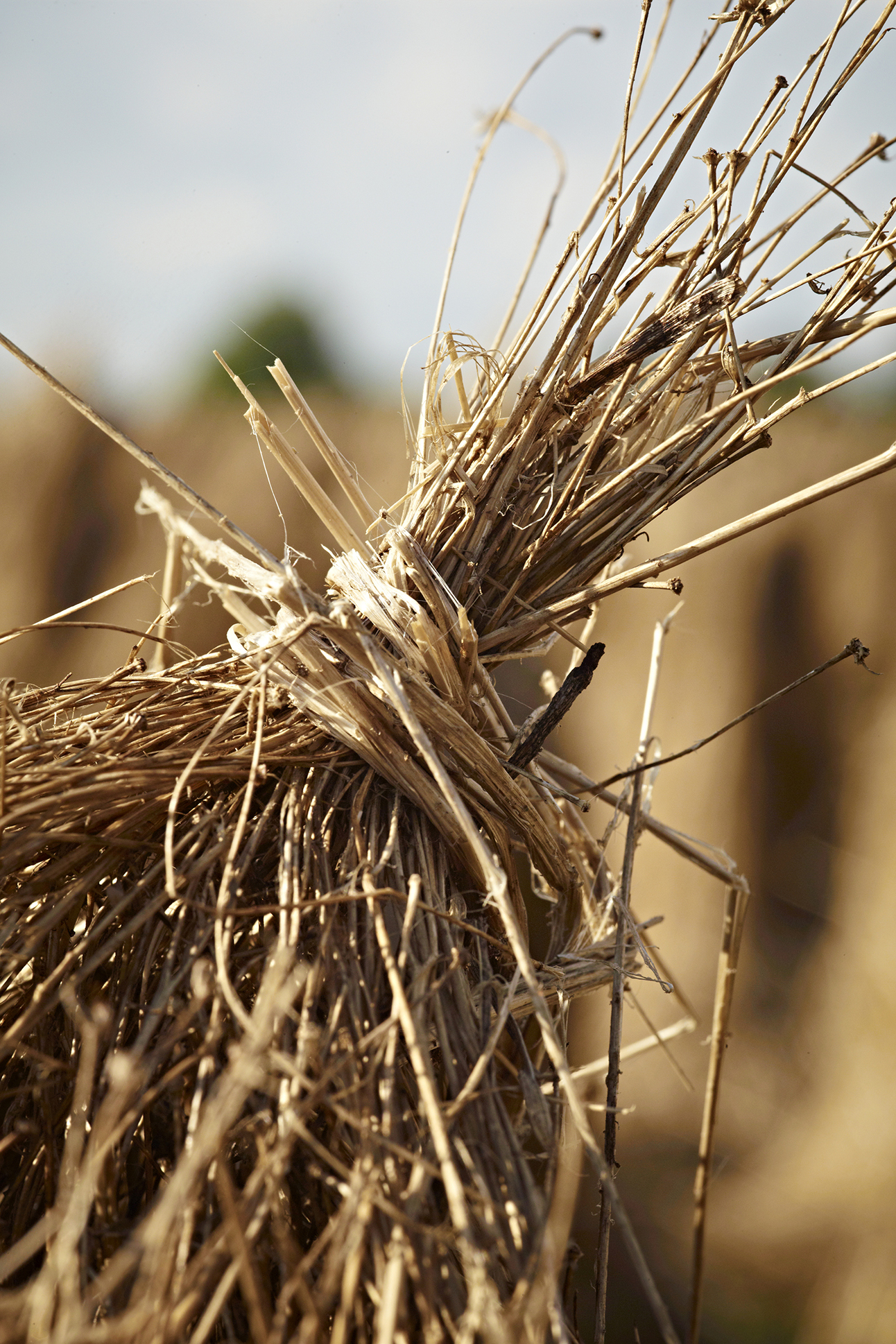
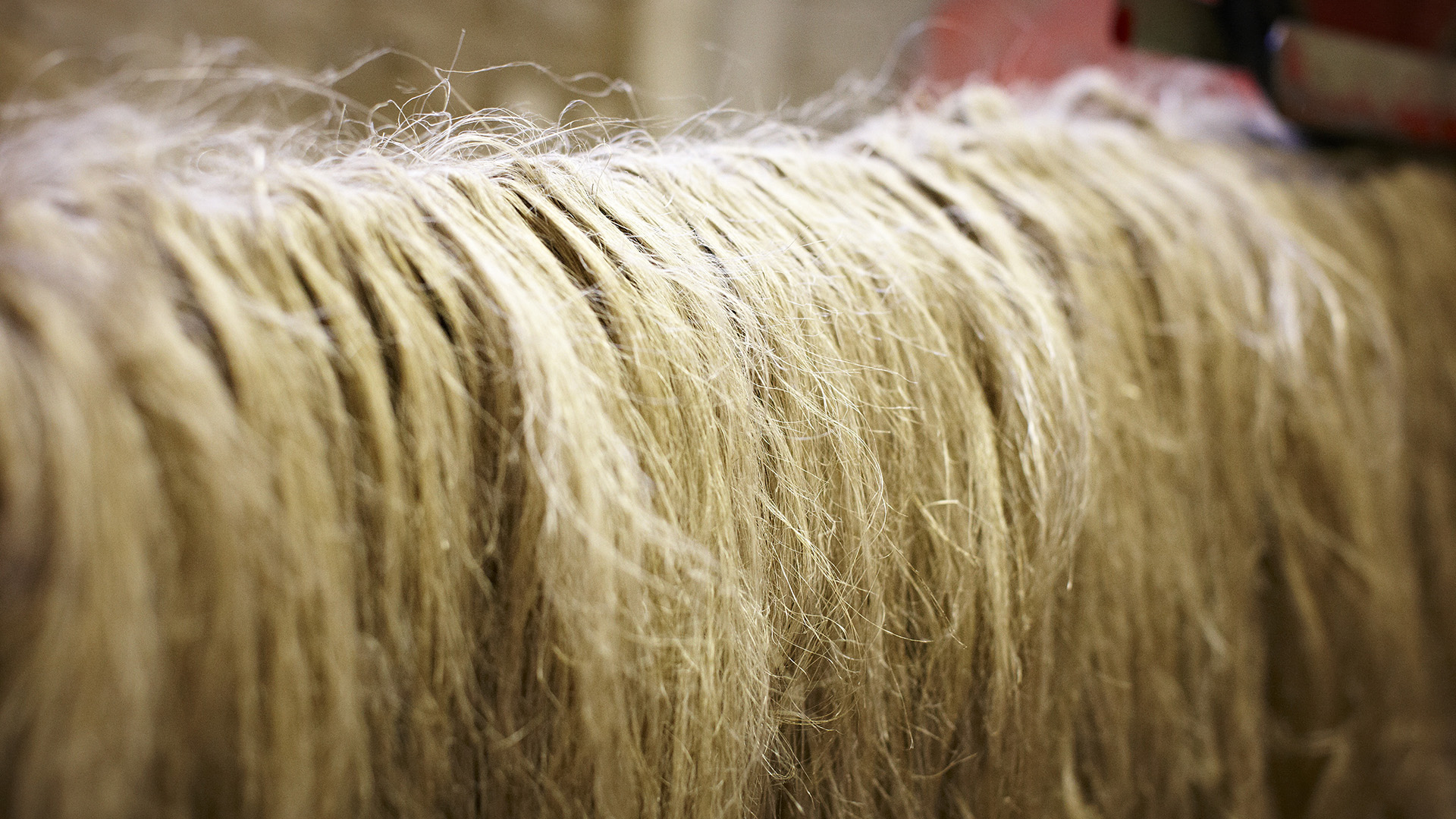
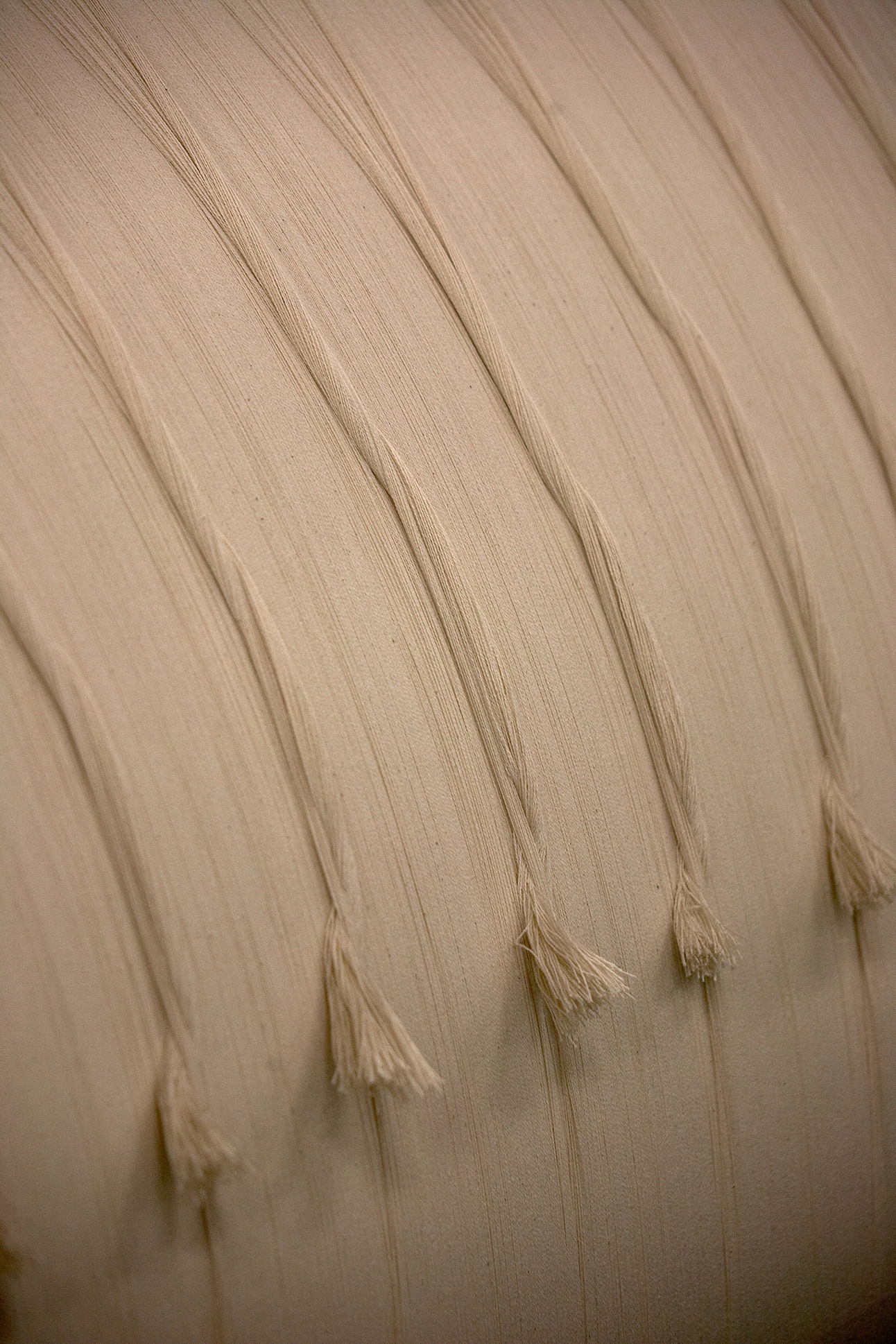
